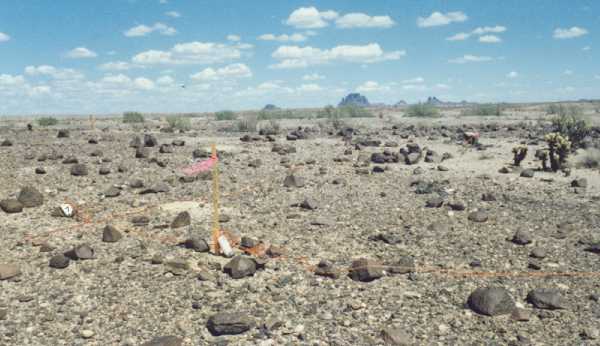
3D E-SCAN's
30-times to
100-times higher signal performance means that getting sufficient ground contact for current injection is that much easier than for conventional survey array electrode installations. Usually, no extra electrode preparations (e.g. digging pits) are needed in establishing sufficient current electrode contact, even in areas where
conventional surveys have failed for this reason.
Conventional surveys often have to resort to digging pits for burying metal foil (with many liters of salt water) in order to get enough current into the ground. No 3D E-SCAN survey conducted to date has needed more than two steel stakes (with a litre of salt water), and never more than 2 amperes of current, to achieve full signal quality at the desired depths of investigation.
Even where the brute power of E-SCAN's 7.5 kilowatt transmitter is needed to drive a ragged current into extra-dry conditions, special waveform synchronization manages the
irregular waveform shapes caused by partially arc-delivered current, ensuring no loss of measured data integrity.
Above, right: June through August in southeast California and southwest Arizona is very hot. While the 3D E-SCAN equipment is not affected by high temperatures, this 3D survey had to be operated on some days between 2 A.M. and 9 A.M. to avoid daytime air temperatures of more than 50 degrees C. Visible low in the distance: peaks of the Chocolate Mountains. No vehicles were permitted off-road on this site, meaning that the manual labor of laying wire and installing electrodes (and recovering it all, later) was done on foot by hardy individuals with big canteens.
Time, cost, risk?
Environmental advantage: The ban on vehicles here was part of a set of severe operating restrictions placed on the E-SCAN crew by the US Bureau of Land Management (BLM) El Centro office, as part of permission to work in this restricted preserve for desert tortoises. The El Centro BLM people reacted positively to the ZERO-DISTURBANCE nature of the proposed 3D E-SCAN survey operation (no electrode pits, no surface disturbance, no vehicles), coupled with the downstream advantage of greatly reducing the number of permitted high-disturbance drill pads required to complete effective 3D exploration of the area.
"Hot/dry" technology: At these high desert temperatures, keeping several hundred electrodes watered to preserve contact is a serious issue... quality results depend upon it. Even with plastic evaporation barriers and the benefits of salt in maintaining sufficient moisture, electrodes can dry to the point where their contact resistance seriously affects data that are acquired at that site.
3D E-SCAN control software has a proprietary electrode contact management system that can routinely evaluate contact resistance at every electrode across the entire grid, without causing the disruptions typical of simple ohm-meter resistance checks. Electrode sites needing a shot of water are flagged and reported for crew action.
Better still, while waiting for such sites to be watered later in the day, the program can actually measure the
undisturbed effective impedance of the electrode
under millivolt signal conditions, to allow acquisition of a fully corrected measurement from the dry-contact electrode. This is an example of the depth of system management technology that is employed to keep 3D E-SCAN producing
verifiable quality results, uninterrupted, in virtually any terrain conditions on earth. It's a benefit of having over three decades of accumulated technological development and hands-on field experience in large scale (hundreds of electrodes) 3D and LINEAR survey operation and management.
Left: Special equipment. Hard desert soil conditions can make summer electrode installation as difficult as dealing with -40 degree frozen ground. A Pionjar "plugger" is adapted to drive 1/2 inch and 5/8 inch (13, 16 mm) stainless steel electrodes into the hard ground.
All of the smaller adapters and tools have colorful tethers attached so that wherever they are dropped, they remain easy to locate.
Should deeper electrode penetration be needed, Crone Geophysics also has a
Vibra-Core soil drill rigged up with electrode adapters, on an ATV, with the capability of driving an electrode even deeper, e.g. for current delivery below a hard, resistant
caliche layer.
100 times higher signal than for dipole-dipole survey array measurements
made to the same depth of investigation (Ze) with the same level of injected current.
30 times higher signal than for pole-dipole survey array (including ORION 3D)
measurements made to the same depth of investigation (Ze) with the same level of injected current.
Transmitter-delivered current is digitized and recorded over exactly the same integration intervals as the measured signal. This means that if current pulses are irregularly tapering off due to electrode contact heating, the measured voltage is exactly correlated (for every pulse) so that the stacked signal/current measurement remains free of error.
Result: Precisely current-normalized, high-quality data from difficult current-injection conditions, with no need for real-time vigilance or special action on the part of the field operator.
Applying an ohm-meter (like the one on the front panel of most commercial IP/resistivity receivers) to an electrode in poor contact conditions may show an acceptably low resistance (under the the 1.5 to 6 volts ohm-meter stimulation) that is not present when ordinary millivolt or microvolt signal levels are present. This failed test can lead to acceptance, without warning, of high-loss signals as normal signals that are then (falsely) interpreted as conductive ground conditions.
The application of 1.5 to 6 volt ohm-meter voltages can upset the electrode-earth interface dynamics, setting up a current-driven electro-chemical voltage offset that may take minutes to decay and settle to zero. That will slow survey progress and tend to inhibit the routine use of ohm-meter contact testing. E-SCAN measures the electrode contact resistance as it actually occurs at the microvolt signal level, ensuring that even where dry-contact signal attenuation (loss) is taking place, that attenuation level is quantified and documented. A real-time correction function can be enables, to restore the degraded measurement to its corrected good-contact level. Meantime, crew can be alerted to service that electrode (add some salt water, pound it deeper) when convenient. With these tools, Crone E-SCAN survey crews can safely and efficiently manage field surveys that employ many hundreds of electrodes in adverse conditions of any kind.
This project would have been easier on crew and equipment if it had started as planned in January, instead of in June's maximum sunshine.
Time: Completed on schedule.
Cost: Fixed budget, no additional charges allowed.
Risk to client: Zero. All risks to contractor.